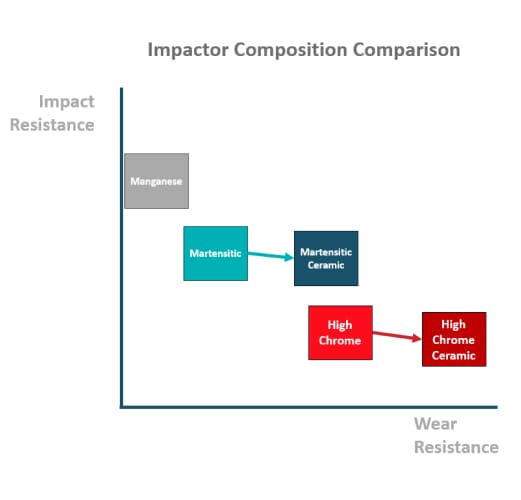
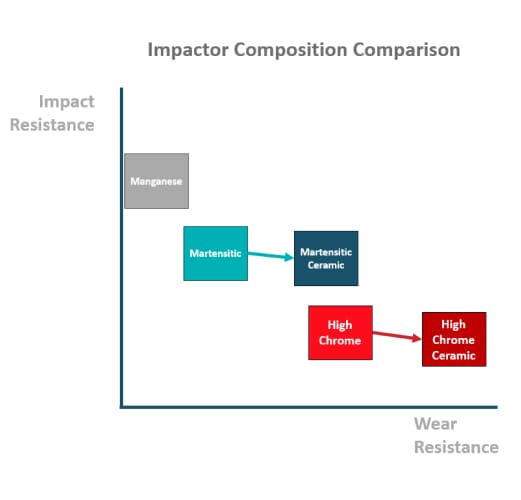
Understanding the impactor
In the construction and mining sectors, one piece of machinery has gained considerable attention for its versatility and performance: the impactor (the Horizontal Shaft Impact Crusher). Curiously, New Zealand has become an outlier in its extensive adoption of impact crushers, possibly because resourceful operators prefer a versatile machine that has the ability to both shape and size material?
Despite their popularity, these crushers are frequently misused, often running at higher operational costs than necessary due to a lack of awareness about efficient operational options and wear part selection. Understanding this is essential to fully leverage the benefits of impact crushers while mitigating their long-term costs.
If you own a Horizontal shaft impact crusher, your most important selection of wear parts are the blow bars (or hammers) and apron bars.
Selecting your wear parts
The 2 most popular types of castings to choose from is martensitic steel, and high chrome. Another option is Manganese steel, however there are only rare occasions where they would be recommended due to being outdated by superior modern technology in martensitic steel and high chrome.
Martensitic steel is a common selection for operators crushing concrete or primary crushing, due to having a good balance between impact resistance, wear resistance and cost. Whereas high chrome is significantly harder and is recommended for harder rock and abrasive environments. However as the metal becomes more wear-resistant, they are also more brittle, making it less resistant to impact, which is a trade-off each customer must consider as impact resistance is important for operators that may have steel or oversized material inadvertently entering the impactor.
To further enhance the abrasion resistance, ceramic inserts can be embedded into the bars to further extend the life of the blow bars, in some cases up to twice the life. They can increase the life of blow bars without sacrificing toughness so the primary factor to consider is the increase in material cost.
In short, the main questions to ask when selecting your impactor parts and overall crushing setup includes:
What are the abrasive and hardness properties of the infeed material?
What is the size of infeed? What is preventing oversize material from entering the crusher?
What is the risk of foreign metal objects entering the crusher? (Is there a tramp metal magnet?)
Investigating these questions will help you minimise your lifetime spending in your impact crusher significantly and reduce the risk of sudden and expensive breakages in your impactor.
Interested in impact crushers? Contact Sanland Equipment today to discover why we have a track record of providing the best cost per ton solution in the country for impactors of all makes and models.